The world cannot ignore the need for circularity. We must move toward a society that doesn’t consume more raw materials than the earth can provide. With Purgatoria, we aim to do our part. We remain committed to the proper functioning and processing of the ICABUS and all waste streams it generates.. Read about our personal motivation here.
ICABUS as a force for sustainability
ICABUS technology is designed to improve the efficiency of the recycling process by separating different types of waste from the fibers, resulting in reduced energy consumption, less waste, and renewability through a sustainable end product and reduced environmental impact.
Fermentation and biogas production
The pulp resulting from the sieving process can be fermented to produce biogas (40% more biogas than surplus sludge alone), or used as a carbon source for phosphate and nitrogen removal.
Contribution to circular economy
The harvested toilet paper fibers can be reused to make new sustainable products, closing the value chain and contributing to a circular economy.
Improved water purification
The ICABUS reduces the undissolved components in wastewater by 30%, increasing sludge activity and contributing to the effectiveness of phosphate and nitrogen removal. The system also reduces the need for aeration energy by 14% and decreases the amount of surplus sludge by 20%.
CO₂ reduction
The ICABUS contributes to a reduction of approximately 1,300 kilograms of CO₂ per ton of sieved material, which also makes the system an environmentally friendly choice.

The ICABUS is a technology mainly used in the paper industry for separating paper fibers from contaminants such as micro-contamination and macro-contamination
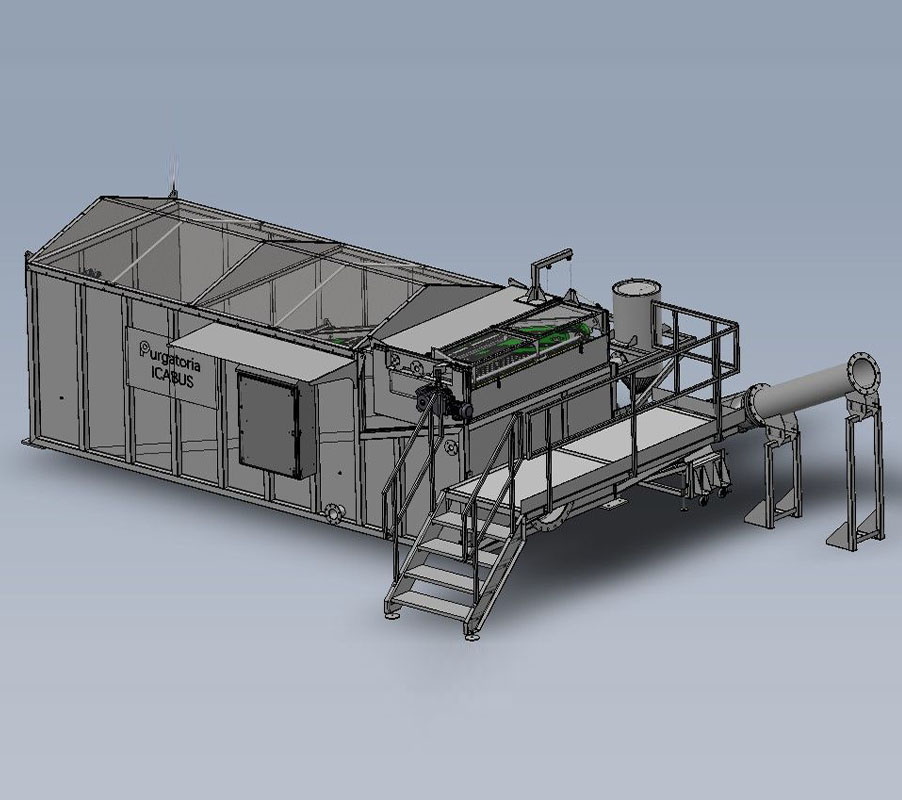
Energy consumption
For the treatment of 700 – 1000 m3/hr we use a 250 Watt motor to power the brushes. Due to the low speed of the brushes on the sieve, a huge power transfer is possible, meaning that this small motor is perfectly capable of propelling the brush holders. In addition, the pump motor for the discharge of the pulp requires only a maximum power of about 1.5 kW to pump the pulp over long distances and heights. By comparison, a belt sieve (max 400 m³/hour) requires 15 kW of compressed air to keep the sieve clean. So the specific energy consumption is 250/1000 vs 15,000/400. You do the math!